The Definitive Guide for Alcast Company
The Definitive Guide for Alcast Company
Blog Article
How Alcast Company can Save You Time, Stress, and Money.
Table of ContentsThe Best Strategy To Use For Alcast CompanyThe 7-Minute Rule for Alcast CompanyAbout Alcast CompanyAlcast Company - The FactsThe Facts About Alcast Company RevealedIndicators on Alcast Company You Need To Know
The refined difference depends on the chemical material. Chemical Contrast of Cast Aluminum Alloys Silicon promotes castability by minimizing the alloy's melting temperature level and improving fluidity during casting. It plays an essential duty in enabling complex molds to be filled up accurately. Additionally, silicon contributes to the alloy's strength and wear resistance, making it beneficial in applications where resilience is crucial, such as automotive components and engine components.It also boosts the machinability of the alloy, making it simpler to refine right into ended up items. In this method, iron adds to the overall workability of aluminum alloys.
Manganese contributes to the strength of aluminum alloys and boosts workability. Magnesium is a light-weight element that gives toughness and effect resistance to aluminum alloys.
Alcast Company Can Be Fun For Everyone
Zinc boosts the castability of aluminum alloys and aids manage the solidification procedure during spreading. It improves the alloy's strength and firmness.
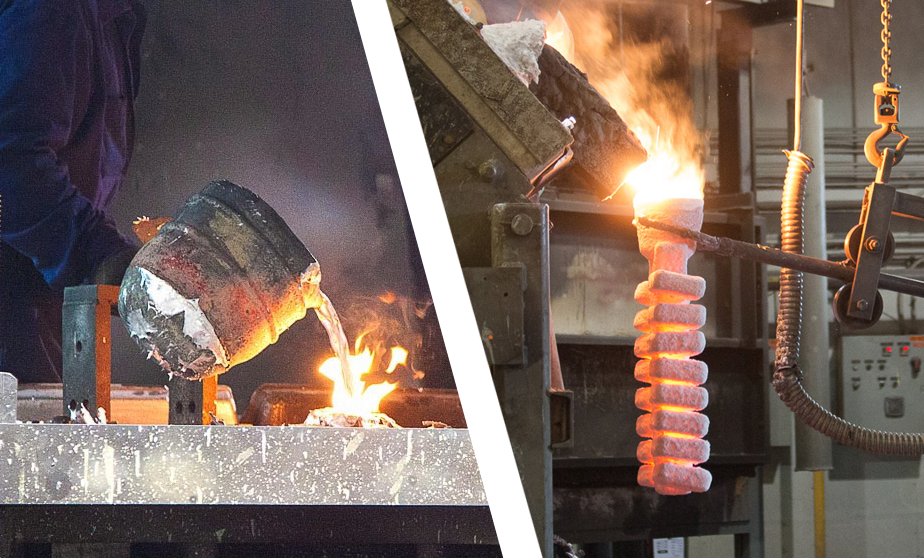
The key thermal conductivity, tensile toughness, return stamina, and elongation vary. Among the above alloys, A356 has the highest possible thermal conductivity, and A380 and ADC12 have the least expensive.
The Greatest Guide To Alcast Company

In accuracy spreading, 6063 is fit for applications where detailed geometries and top quality surface area finishes are extremely important. Instances include telecommunication units, where the alloy's premium formability enables smooth and visually pleasing layouts while maintaining structural honesty. In the Lights Solutions industry, precision-cast 6063 components produce classy and efficient lights fixtures that need complex forms and great thermal efficiency.
The A360 displays premium prolongation, making it excellent for facility and thin-walled parts. In accuracy casting applications, A360 is fit for industries such as Customer Electronic Devices, Telecommunication, and Power Devices.
The Ultimate Guide To Alcast Company
Its distinct properties make A360 a useful selection for accuracy spreading in these industries, improving product toughness and top quality. aluminum casting company. Aluminum alloy 380, or A380, is a commonly utilized spreading alloy with a number of unique attributes.
In accuracy spreading, light weight aluminum 413 beams in the Customer Electronic Devices and Power Equipment markets. It's typically used to craft detailed parts like mobile phone real estates, camera bodies, and power device coverings. Its precision is exceptional, with limited resistances up to 0.01 mm, ensuring remarkable item setting up. This alloy's premium deterioration resistance makes it a superb option for exterior applications, ensuring long-lasting, resilient products in the discussed sectors.
Little Known Questions About Alcast Company.
The light weight aluminum alloy you select will substantially affect both the casting procedure find out here now and the residential properties of the final product. Because of this, you should make your decision meticulously and take an informed technique.
Identifying the most suitable aluminum alloy for your application will certainly imply evaluating a large variety of attributes. These comparative alloy attributes follow the North American Pass Away Spreading Association's standards, and we've separated them right into two categories. The first category addresses alloy qualities that impact the manufacturing process. The second covers qualities impacting the properties of the end product.
5 Easy Facts About Alcast Company Explained
The alloy you select for die casting straight impacts several elements of the spreading procedure, like just how simple the alloy is to work with and if it is prone to casting issues. Hot breaking, also called solidification cracking, is a normal die casting issue for aluminum alloys that can result in inner or surface-level splits or splits.
Certain light weight aluminum alloys are extra susceptible to hot cracking than others, and your choice must consider this. It can harm both the actors and the die, so you should look for alloys with high anti-soldering buildings.
Corrosion resistance, which is currently a notable quality of light weight aluminum, can differ substantially from alloy to alloy and is a necessary characteristic to consider depending upon the ecological problems your item will be exposed to (Casting Foundry). Wear resistance is one more property commonly sought in aluminum items and can differentiate some alloys
Report this page